运用 Cipher 揭示微观尺度上的锂含量
导言
从为移动电子设备和汽车提供动力的锂离子电池到轻量化结构合金,含锂化合物和合金是21世纪许多重要技术的关键材料。这些领域已经取得了长足进展,但仍旧缺少在微观尺度上确定锂成分的表征方法。通常,在扫描电镜(SEM)中我们使用能量弥散X-射线谱(EDS)进行微区分析。但这一表征手段无法对原子序数 (Z) < 4 的元素进行分析,由于这些元素发出的特征X-射线 (例如, Li K ~55 eV) 很容易就被样品本身或氧化层/污染层吸收,而需要非常特殊的探测器才能探测到。即便如此,由于锂的荧光产额本身也依赖于化学键合状态,从而无法对锂进行定量测量,并且只能达到 ~ 20 wt. %的检出限,这些问题对锂的分析带来了严重问题 [1]。进来有研究表明通过这些特殊探测器得到的锂元素分布图的可靠性存疑 [2]。
最近,来自 LKR/AIT 的研究人员通过成分差异法,结合 EDS 和定量背散射电子成像 (qBEI),展示了在 SEM 中对锂进行定量分析的能力 [3,4]。对于原子序数 Z = 4 – 94 的元素通过 EDS 分析获得定量信息,而通过 qBEI 则能够确定平均原子质量(qBEI 信号是原子序数的函数,对于 Z = 1 – 94)。假设轻元素(Z = 1 – 3)都是锂,它所占的比例可以通过计算得到,如参考文献中对 MgLi 合金所进行的分析。研究表明通过这种成分差异法计算锂含量 (Li-CDM),能够以可接受的精度 (~1 wt. %) 检测到 < 5 wt. % 的锂。
Gatan 和 EDAX 推出的 Cipher™ 系统将 EDAX Octane Elite 或 Elect Super EDS 探测器与 Gatan OnPoint™ 背散射电子探测器整合,加上 DigitalMicrograph®️ 软件中的成分差异分析模块,能够对样品中的锂成分进行定量测量。在本文中,我们在一系列非金属材料中评估了 Li-CDM 方法的精确度,并详述了通过 Cipher 对具有化学计量比的铝酸锂和常用于锂离子电池正极的镍锰钴三元锂氧化物颗粒进行分析的最新结果。
材料与方法
通过 Cipher 对 55 个样品(Micro-Analysis Consultants Ltd)进行了定量背散射电子测量。这些样品包括了元素单质、矿物、半导体和合金材料,平均原子序数介于 4 – 83。这些样品经由机械抛光,并通过 PECS™ II 系统进行了 2.0 nm 厚的镀碳以避免 SEM 中产生荷电累积。
通过 Cipher 对两个商用样品进行了定量锂分析 – 高纯(>99.99 %) LiAlO2 (100) 晶体基片以及镍锰钴氧化物三元锂(NMC)颗粒,其名义 Ni:Mn:Co 比例 8:1:1,含锂 5.7 wt. %(大约 25 at. %)。
样品通过 Gatan Ilion®️ II 或 PECS™ II 宽束氩离子研磨进行抛光,并镀上 2.0 nm 的碳膜以避免荷电现象。在样品制备前,将 NMC 811 粉末样品镶嵌在环氧树脂中形成块体样品。通过场发射 SEM 分别在 20 和 25 kV 下采集 EDS 和 qBEI 数据,以确保所有 X-射线线系都得到高效激发,以及一致的信号采样体积。还使用了 Clarity™ 探测器对 NMC 样品进行了电子被散射衍射(EBSD)表征来揭示其晶体结构。
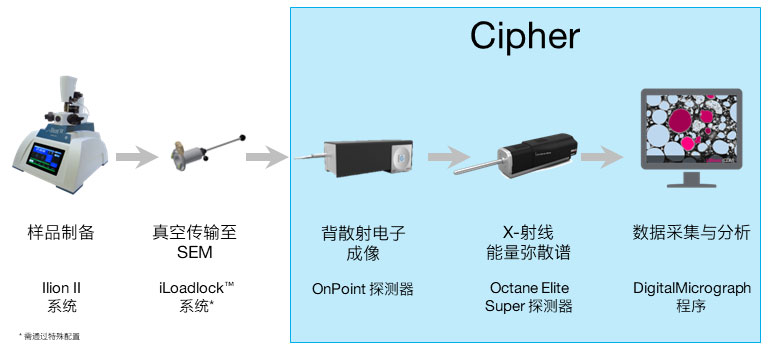
图 1. Cipher 系统使您能够在含锂样品中对锂元素进行定量分析,为您的锂研究“充电”。
结果与讨论
评估 Li-CDM 方法对化合物材料的适用性
qBSE 信号作为平均原子序数 qBSE 信号作为平均原子序数 的函数,在图 2 中进行了绘制,
通过改进的公式 (1) 计算得到(参考 [5]):
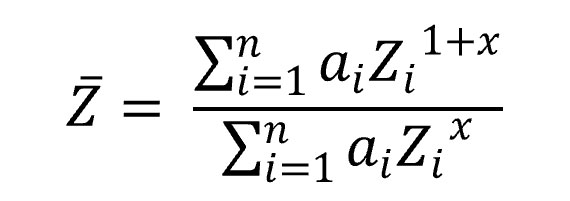
公式 1
ai 代表了元素 i 的原子占比,x ≃ 0.7。同其它文献一致(例如 [6]),qBSE 信号拟合至下面的函数:
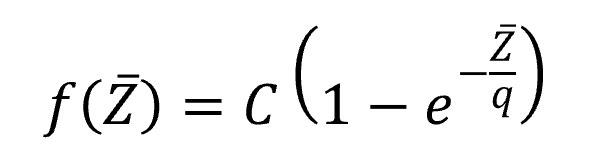
公式 2
C 和 q 是与 SEM 和探测器设置相关的常数。
对于 < 40的化合物,实验数据同公式 2 的指数函数吻合的非常好,几乎没有例外的数据点。但是,对于
&> 40 的材料,尽管数据点依旧符合函数大体趋势,但数据点增加的分散性表明在此情况下通过 Li-CDM 计算可能带来更大的不确定性。尽管如此,可以确定对
< 40 的各种金属和非金属样品来说,Li-CDM 是合适的方法。
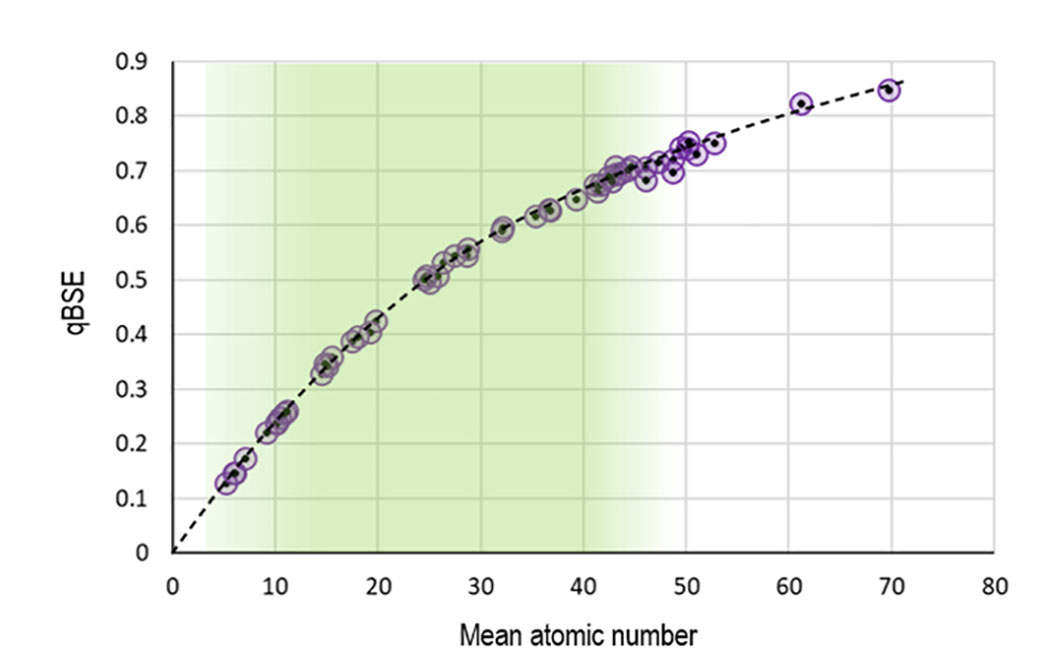
图 2. 归一化的背散射电子图像灰度等级与平均原子序数的关系图。化合物材料的平均原子序数计算采用了改进过的公式 (1)。圆圈为实验数据,虚线为来自公式 (3) 的指数拟合函数。
评估铝酸锂中的锂含量
使用 Cipher 来确定铝酸锂样品中的锂含量。成分分析结果总结在表 1 中。分析得到的锂含量为 22.6 ± 3.5 at. % (9.5 ± 1.7 wt. %);与名义含量 25.0 at. % (10.5 wt. %) 相差在 2.4 at. % 以及仅仅 0.9 wt. % 内。
Li | Al | O | |
化学计量比 | |||
At. % | 25.0 | 25.0 | 50.0 |
EDS 结果 | |||
At.% | - | 29.6 | 70.4 |
标准差 | - | 1.6 | 5.1 |
成分差异法获得锂含量 | |||
At. % | 22.6 | 22.9 | 54.6 |
标准差 | 3.5 | 1.0 | 4.0 |
表 1. LiAlO2 样品的元素定量结果
评估锂离子电池正极材料的锂含量
所分析的 NMC 811 粉末由大体为球形的直径覆盖 5 – 30 µm 的’二级‘ 颗粒构成。这些二级颗粒是由更小的 ’一级‘ 颗粒聚集构成,可通过电子背散射衍射(EBSD)采集的晶体取向分布图(图 3)显示出来。通过 EDAX Clarity EBSD 探测器采集的取向图表明这些一级颗粒的尺寸在 200 – 2,0000 nm 范围并具有随机晶体取向,一级颗粒间没有或仅有非常少的间隙。
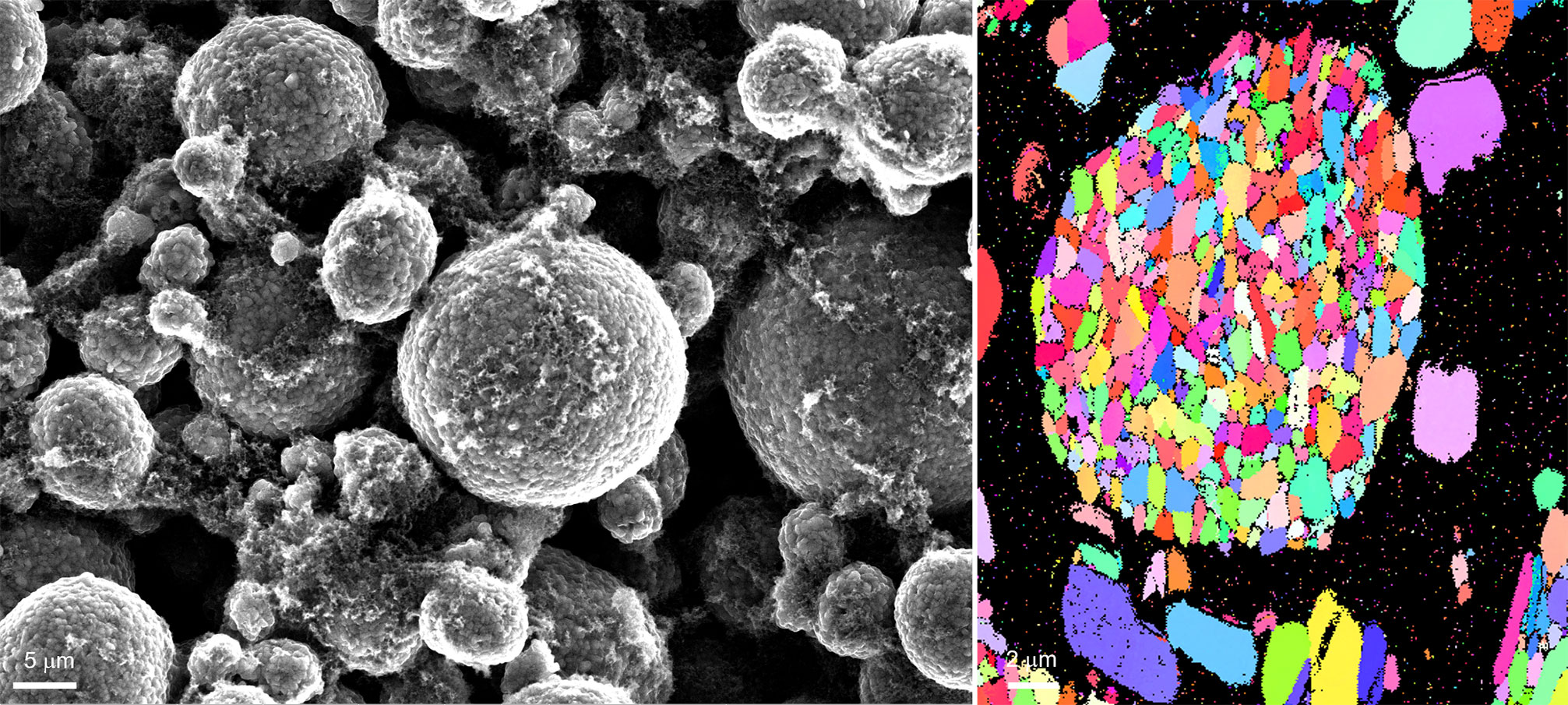
图 3. 镍锰钴氧化物三元锂粉末样品的代表性二次电子像和 b) 取向分布图
在 NMC 颗粒上选定位置的 EDS 定量分析表明 O、Ni、Mn 和 Co 在颗粒内及颗粒间几乎不存在显著的成分起伏 (表 2)。没有其它高于检出限的元素存在。实验确定的 Ni:Mn:Co 比例 8.07:1.00:1.01 与名义值 8:1:1 符合。
名义含量 (at. %) | ||||||||
Li | O | Ni | Mn | Co | Ni | Mn | Co | |
- | 66.7 | 26.7 | 3.3 | 3.3 | 8.00 | 1.00 | 1.00 | |
实验值 (at. %) | ||||||||
O | Ni | Mn | Co | Ni | Mn | Co | ||
Spot 1 | 73.3 | 21.3 | 2.7 | 2.7 | 7.89 | 1.00 | 1.00 | |
Spot 2 | 74.4 | 20.3 | 2.6 | 2.6 | 7.81 | 1.00 | 1.00 | |
Spot 3 | 72.8 | 21.8 | 2.7 | 2.7 | 8.07 | 1.00 | 1.00 | |
Area 1 | 73.0 | 21.4 | 2.7 | 2.9 | 7.93 | 1.00 | 1.07 | |
Area 2 | 71.7 | 22.9 | 2.7 | 2.7 | 8.48 | 1.00 | 1.00 | |
Area 3 | 73.2 | 21.5 | 2.6 | 2.6 | 8.27 | 1.00 | 1.00 | |
Mean | 8.07 | 1.00 | 1.01 |
表 2. 对于6个 NMC 颗粒的定量 EDS 分析。分析位置如图 4 所示.
使用 Cipher 对6个不同的 NMC 颗粒的锂含量进行了测量;分析位置如图 4 所示。测得的平均锂含量为 22.5 at. % (5.7 wt. %),在名义含量 7.3 ± 0.3 wt. % 的 ~1.5 wt.% 偏差以内。
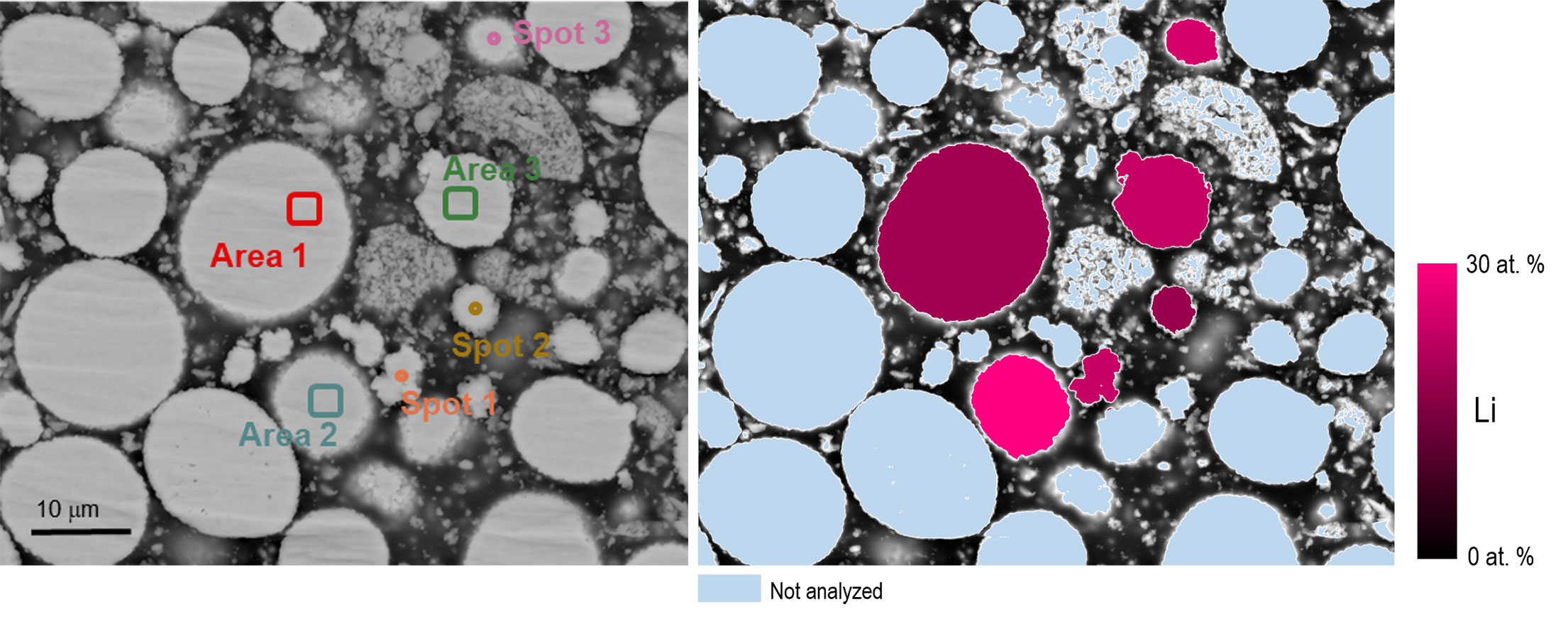
图 4. a) 定量背散射电子像,灰度值可直接同平均原子序数

这是推动电池材料分析的一个重要进展,我们得以在传统 SEM 中确定正极材料的充电状态。在本例子中,~25 at. % 的锂含量对应于电池完全放电的状态。
小结
在具有化学计量比的化合物样品中通过成分差异法获得锂含量。在高纯铝酸锂晶体基片中测得的锂含量 9.5 wt. %,与化学计量值相比差异小于 ~1 wt. %, 与之前在金属样品中报导的精确度类似 [2]。
并且,我们得以首次在传统扫描电镜中对 NMC 正极材料的锂含量进行了测量。实验测得的平均锂含量为 22.5 at.%,对应此材料在电池中的未充电状态。上述结果证明了 Li-CDM 在更广泛材料类型中的适用性,从而打开了运用 Cipher 对含锂电池材料表征的令人激动的可能性。
参考文献
- P. Hovington et al., Scanning 38 (2016) p. 571–578
- R. Gauvin and N. Brodusch, Microsc. Microanal. 28 (Suppl 1), 2022. doi:10.1017/S1431927622002847
- J.A. Österreicher et al., Scripta Materialia 194 (2021) 113664
- Austrian Patent Application A 50783/2020
- J. Donovan et al., (2003) Microsc. Microanal. 9, p. 202. DOI: 10.1017/S143192760030137
- A. Garitagoitia Cid et al., Ultramicroscopy 195 (2018) 47
- https://www.edax.com/-/media/ametekedax/files/eds/ technical_notes/3d%20analysis%20of%20eds%20data.pdf
- D. Kaczmarek, Scanning Microscopy 12 (1) (1998) p. 161-169